Ultra Pure Titanium
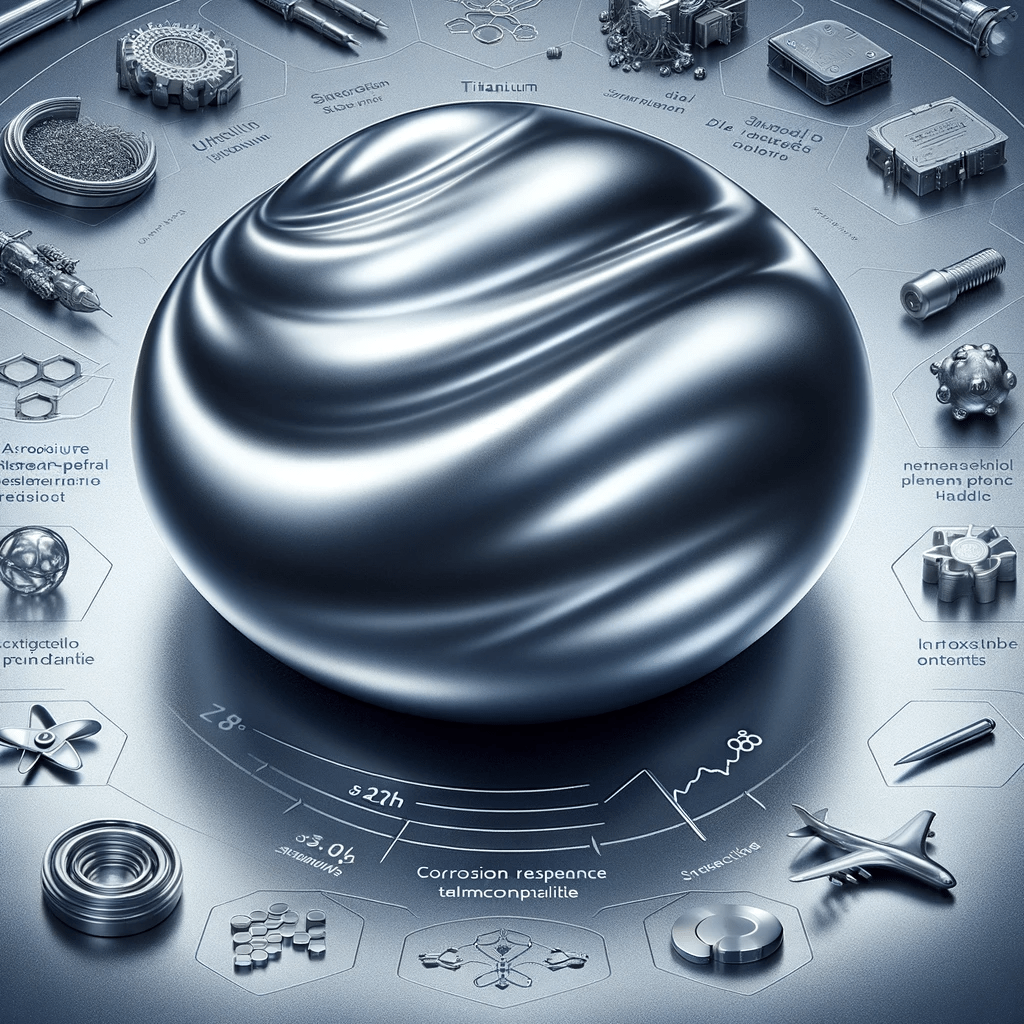
Ultra-pure titanium has a silvery-gray metallic appearance, similar to other pure metals such as silver or aluminum. It has a smooth and shiny surface when polished or machined, and can also have a slightly bluish or yellowish tint depending on the lighting conditions and surface finish.
The surface of ultra-pure titanium is typically free of visible impurities or defects, due to its high level of purity. However, it can still be susceptible to scratches, dents, and other forms of physical damage, which can affect its appearance and performance.
Ultra-pure titanium is a relatively dense metal, with a density of around 4.5 g/cm³. It is also relatively lightweight compared to many other common metals, such as steel or copper, which makes it a popular choice in aerospace and other weight-sensitive applications.
In terms of its physical properties, ultra-pure titanium is a ductile and malleable metal, which means that it can be easily shaped or formed into different geometries without cracking or breaking. It is also a good conductor of heat and electricity, although not as good as some other metals such as copper or aluminum.
Plasma-Facing Components
Titanium is known for its excellent resistance to corrosion and erosion, which makes it a popular choice for plasma-facing components in fusion reactors and other high-temperature plasma environments. In these applications, the titanium components are exposed to high-energy plasma particles, which can cause significant damage and wear over time. However, the high corrosion resistance of titanium can help to mitigate these effects and extend the lifespan of the components.
Additionally, titanium can also be used in certain plasma deposition processes, such as physical vapor deposition (PVD) and chemical vapor deposition (CVD), where it can be used as a substrate or target material. In these processes, a high-energy plasma is used to deposit a thin film of material onto a substrate, such as a semiconductor wafer or a metal component. Titanium and its alloys can be used as substrate materials due to their high purity, low reactivity, and compatibility with the deposition process.
3D Printing
Ultra-pure titanium can be used in 3D printing. In fact, 3D printing, also known as additive manufacturing, is becoming an increasingly popular method for producing parts and components made from ultra-pure titanium and other metals.
There are several additive manufacturing techniques that can be used to produce parts from ultra-pure titanium, including powder bed fusion and directed energy deposition. These techniques involve using a high-powered laser or electron beam to selectively melt and fuse layers of titanium powder, gradually building up the part layer by layer.
The advantages of 3D printing with ultra-pure titanium include the ability to produce complex geometries and customized parts with high precision and accuracy, without the need for expensive tooling or molds. It also allows for faster prototyping and reduced material waste compared to traditional manufacturing methods.
However, it should be noted that 3D printing with ultra-pure titanium can be challenging due to the material’s high melting point and low thermal conductivity. It also requires specialized equipment and expertise to ensure that the parts are produced with the desired properties and quality.
Ultra-pure titanium can be used in 3D printing, and this method offers several advantages for producing complex and customized parts. However, it requires specialized equipment and expertise to ensure the parts are produced to the desired quality and properties.
5N titanium
5N titanium is a term used to describe titanium that has a purity level of 99.999%, meaning it contains less than 0.001% of impurities. The “N” in 5N stands for “nines,” which is a common way to express the purity level of a material, with each “nine” indicating an additional decimal place of purity.
In the case of 5N titanium, the material has undergone extensive refining processes to remove impurities, resulting in a very high level of purity. This level of purity is typically required for high-tech applications such as aerospace, medical implants, and electronics, where the material’s unique combination of strength, lightweight, and resistance to corrosion make it an ideal choice.
The science behind ultra-pure titanium involves a combination of materials science, chemistry, and engineering principles.
Titanium is a chemical element with the symbol Ti and atomic number 22. It is a strong, lightweight metal with excellent corrosion resistance, making it a popular material for a variety of applications. However, titanium is rarely found in its pure form in nature and is typically extracted from minerals such as ilmenite and rutile.
To create ultra-pure titanium, the extracted titanium undergoes a series of refining processes. The first step involves reducing the titanium oxide to pure titanium using a process known as the Kroll process. The titanium sponge produced from the Kroll process is then further refined through a series of chemical and physical treatments to remove impurities.
One common technique used to purify titanium is called the Van Arkel–de Boer process, which involves reacting titanium tetrachloride with a metal like magnesium or sodium at high temperatures. The resulting product is then distilled under vacuum to remove any remaining impurities.
Another method of purifying titanium involves using high-temperature plasma arc melting, which involves melting the titanium in a vacuum and subjecting it to a plasma arc to remove impurities.
Once the titanium has been purified to the desired level, it can be formed into various shapes and used in a variety of applications. The properties of ultra-pure titanium, including its strength, corrosion resistance, and biocompatibility, make it a valuable material in industries such as aerospace, medical devices, and electronics.
Resistant to Corrosion, Particularly in Environments such as Seawater
Ultra-pure titanium has a number of advantages over lower-purity titanium alloys. For example, it is more resistant to corrosion, particularly in environments such as seawater, where other metals might corrode quickly.
This is due to the formation of a thin, protective oxide layer on the surface of the metal, which acts as a barrier to further corrosion. In seawater, this oxide layer is particularly important, as seawater contains a high concentration of chloride ions, which can be highly corrosive to many metals.
However, titanium’s oxide layer is able to resist corrosion even in the presence of chloride ions, making it a popular choice for marine and offshore applications. It is also more biocompatible, which means that it is less likely to cause adverse reactions when used in medical implants or other applications involving contact with the human body.
Higher Strength-to-weight Ratio
In addition, ultra-pure titanium has a higher strength-to-weight ratio than many other metals, making it a popular choice in aerospace and other high-performance applications. However, ultra-pure titanium can also be more expensive and difficult to work with than lower-purity titanium alloys, due to its higher purity and more stringent processing requirements.
Here is a table comparing the strength-to-weight ratio of ultra-pure titanium with other common metals:
Metal | Density (g/cm³) | Tensile Strength (MPa) | Yield Strength (MPa) | Strength-to-Weight Ratio (kN·m/kg) |
---|---|---|---|---|
Titanium (Ultra-pure) | 4.51 | 880 | 828 | 196 |
Aluminum (7075-T6) | 2.81 | 572 | 503 | 204 |
Steel (AISI 4130) | 7.85 | 670 | 435 | 85.4 |
Magnesium (AZ31B) | 1.78 | 283 | 179 | 159 |
Nickel (Inconel 718) | 8.19 | 1276 | 1103 | 32.9 |
In the case of aluminum and titanium, the two metals have different mechanical properties that can make them more or less suitable for certain manufacturing processes or geometries. For example, titanium is known for its high strength-to-weight ratio and its ability to withstand high temperatures, which makes it a good choice for aerospace applications that require lightweight and durable parts. However, titanium is also known for its poor machinability, which means that it may be more difficult or time-consuming to manufacture complex shapes or features.
The electrical conductivity of ultra-pure titanium depends on its specific alloy and processing method. However, compared to other common metals, such as copper and aluminum, titanium has a lower electrical conductivity. Here is a table comparing the electrical conductivity of ultra-pure titanium with other metals:
Metal | Electrical Conductivity (MS/m) |
---|---|
Titanium (Ultra-pure) | 1.29 |
Copper | 57 |
Aluminum | 37 |
High-temperature Strength and Creep Resistance
Titanium can be used in applications where low electrical conductivity is desired. The electrical conductivity of ultra-pure titanium is lower than that of copper and aluminum, which are commonly used as electrical conductors.
Ultra-pure titanium has a relatively high resistance to heat compared to many other metals, which makes it a popular choice in high-temperature applications. Titanium has a melting point of approximately 1,660°C (3,020°F), which is higher than the melting points of many other common metals, such as aluminum, copper, and steel.
In addition to its high melting point, titanium also has good strength retention at high temperatures, which means that it can maintain its mechanical properties even when exposed to high temperatures. This property makes it a good choice for applications such as jet engine components, where the parts are exposed to extreme temperatures.
That being said, the resistance of ultra-pure titanium to heat can vary depending on its specific alloy and processing method. Some titanium alloys, such as Ti-6Al-4V, are known for their high-temperature strength and creep resistance, which make them suitable for use in even more extreme high-temperature environments.
Here is a table comparing the melting points of ultra-pure titanium with other common metals:
Metal | Melting Point (°C) |
---|---|
Titanium (Ultra-pure) | 1,660 |
Aluminum | 660 |
Copper | 1,085 |
Steel | 1,370 |
Ultra-pure titanium has a relatively high resistance to heat compared to many other metals, which makes it a popular choice in high-temperature applications.