Friction and Cavitation of Trans-Medium Craft
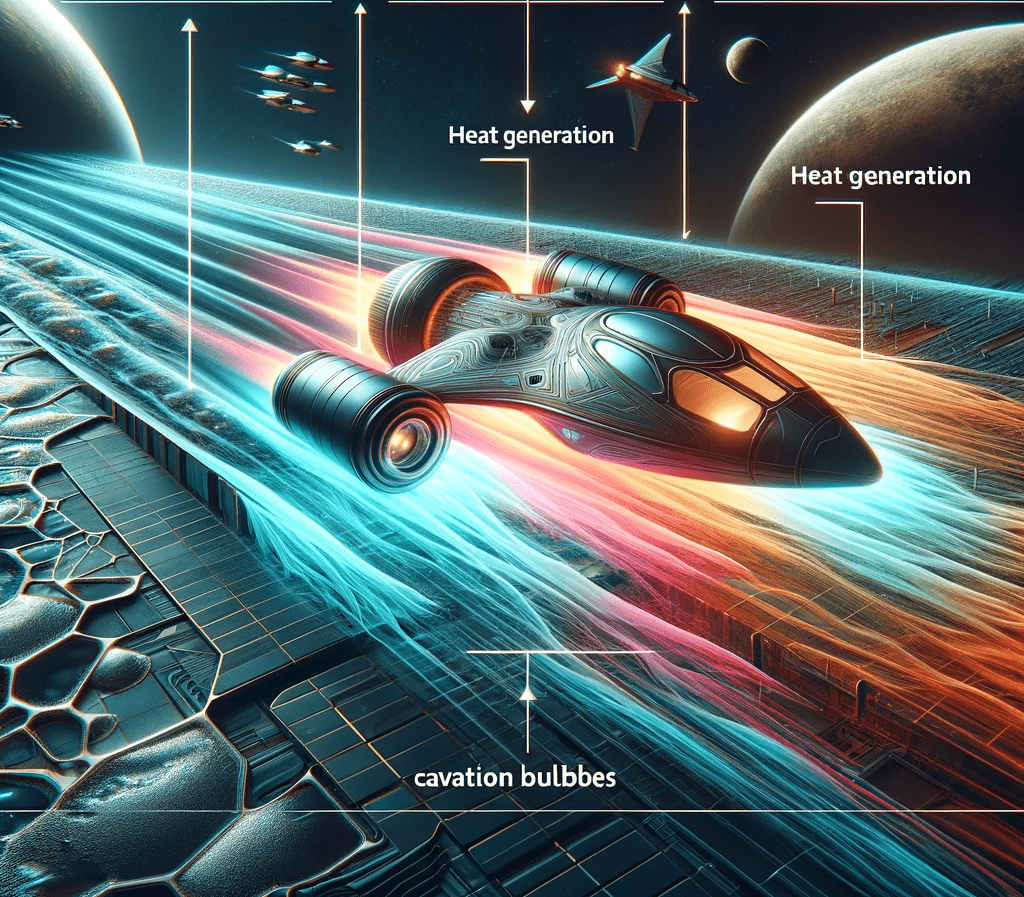
Trans-medium crafts, vehicles designed to traverse both aerial and aquatic environments, grapple with an array of operational intricacies. Among the most formidable challenges are the repercussions of friction and cavitation. As these crafts achieve remarkable velocities, they confront substantial heat due to friction, with the effects being particularly accentuated underwater because of water’s greater density and viscosity. Concurrently, when in water, cavitation introduces further thermal and mechanical adversities. Such extreme conditions raise questions beyond just materials; it suggests that if such crafts exist and operate as proposed, they might employ exotic mechanisms, potentially including some form of shielding, to mitigate these effects or even completely bypass interactions with the environment, perhaps invoking concepts as advanced as interdimensional travel.
Generally, as the speed of an object increases, the drag force (and the associated friction and heat) also increases. For hypersonic speeds (greater than 5 times the speed of sound), the heat generated due to compression of air can be significant and can lead to very high temperatures on the surface of the object.
For instance, the Space Shuttle re-entering Earth’s atmosphere at hypersonic speeds experiences temperatures of about 2,500°F (1,650°C) on its thermal protection tiles. The heat arises not only from friction but also from the compression of air in front of the shuttle.
UFOs, as they’re popularly depicted, often show capabilities beyond our current understanding of physics, including instantaneous changes in direction and velocities far exceeding anything man-made. If a UFO were traveling at these imagined speeds in our atmosphere, the friction would be immense, generating an incredible amount of heat.
- Sea Level: The air is denser, causing more friction and heating. At 12,000 mph, the temperature would likely exceed the melting point of many materials.
- 30,000 ft: This is around the cruising altitude for commercial airliners. The air is less dense, causing less heating than at sea level.
- 60,000 ft: This is above the altitude for most commercial aircraft and entering the range for specialized aircraft like the U-2. The air is much thinner, leading to less aerodynamic heating.
This table provides a snapshot of estimated surface temperatures for an object traveling at varying speeds and altitudes. It further delineates which metals would melt at these temperatures and which would remain intact. Use this as a reference to understand the thermal challenges faced by materials in high-speed scenarios across different altitudinal zones.
Speed (mph) | Altitude (ft) | Estimated Surface Temperature (°C) | Metals That Would Melt | Metals That Would Not Melt |
---|---|---|---|---|
2000 | Sea level | 800 | Aluminum | Copper, Iron, Titanium |
2000 | 30,000 | 350 | – | Aluminum, Copper, Iron, Titanium |
2000 | 60,000 | 150 | – | Aluminum, Copper, Iron, Titanium |
5000 | Sea level | 2500 | Aluminum, Copper, Iron | Titanium |
5000 | 30,000 | 1500 | Aluminum, Copper | Iron, Titanium |
5000 | 60,000 | 750 | Aluminum | Copper, Iron, Titanium |
12000 | Sea level | 4500 | Aluminum, Copper, Iron, Titanium | – |
12000 | 30,000 | 3200 | Aluminum, Copper, Iron | Titanium |
12000 | 60,000 | 2250 | Aluminum, Copper, Iron | Titanium |
For a temperature of 4500°C, most conventional metals and even some refractory metals will melt or be in a weakened state. However, there are a few materials and compounds that can withstand such temperatures, although not necessarily in a metallic form:
- Tantalum hafnium carbide (Ta4HfC5): This is a compound, not a pure metal. It’s believed to have the highest melting point of any known compound at about 4215°C. It’s close to 4500°C but still a bit below.
- Graphene and Carbon Nanotubes: These carbon allotropes don’t melt in the traditional sense but can withstand extreme temperatures. Their sublimation point (where they go directly from solid to gas) is over 3500°C in a vacuum. Their behavior might differ in atmospheric conditions, especially at 4500°C, and they might not remain stable.
- Rhenium: One of the refractory metals with a melting point of 3186°C. While it won’t withstand 4500°C, it’s one of the highest-melting-point pure metals.
- Osmium: Another metal with a very high melting point of around 3033°C.
- Tungsten: A metal with a melting point of 3422°C. It’s often used in light bulb filaments and in environments requiring high temperatures, but it too will melt before 4500°C.
Traveling underwater introduces significantly different challenges than traveling in the air. The density of water is much higher than air, leading to far more resistance. In fact, the high speeds mentioned in the previous table would be almost inconceivable underwater due to the immense resistance and heating caused by cavitation.
Cavitation is a phenomenon where rapid changes in pressure in a liquid lead to the formation of small vapor-filled cavities in places where the pressure is relatively low. When these cavities collapse, they generate intense shockwaves, high heat, and can cause significant damage.
The fastest known underwater vehicle, a torpedo, can reach around 370 mph, and it’s specifically designed for those conditions.
The table below offers a comprehensive overview of the estimated surface temperatures for objects moving at different speeds and depths underwater, emphasizing the metals that would potentially melt at these temperatures. By examining the friction and cavitation implications for trans-medium crafts, it showcases the challenges these crafts face when transitioning between mediums. This serves as both a clear insight into material durability and a concise reference for understanding operational challenges at varying velocities.
Speed (mph) | Depth (ft) | Estimated Surface Temperature (°C) | Metals That Would Melt | Metals That Would Not Melt |
---|---|---|---|---|
2000 | Surface | 4000 | Aluminum, Copper, Iron | Titanium |
2000 | 500 | 4500 | Aluminum, Copper, Iron, Titanium | – |
2000 | 1000 | 5000 | Aluminum, Copper, Iron, Titanium | – |
5000 | Surface | 9000 | Aluminum, Copper, Iron, Titanium | – |
5000 | 500 | 10000 | Aluminum, Copper, Iron, Titanium | – |
5000 | 1000 | 11000 | Aluminum, Copper, Iron, Titanium | – |
12000 | Surface | 18000 | Aluminum, Copper, Iron, Titanium | – |
12000 | 500 | 19000 | Aluminum, Copper, Iron, Titanium | – |
12000 | 1000 | 20000 | Aluminum, Copper, Iron, Titanium | – |
Submarines and torpedoes primarily utilize robust and corrosion-resistant metals for their outer construction. The main hull of submarines is often crafted from high-strength steel alloys like HY-80 or HY-100, designed to withstand profound underwater pressures. Some advanced submarines incorporate titanium, prized for its strength-to-weight ratio and corrosion resistance. Similarly, the shell of torpedoes is generally constructed from stainless steel or other resilient steel alloys. These metals ensure that both submarines and torpedoes can effectively endure the demanding marine environment and maintain their structural integrity during operations.
While our assessment underscores that even our best and most resilient metals, including specialized alloys like HY-80, HY-100, and titanium, cannot withstand the predicted extreme conditions of high-speed trans-medium traversal, it also beckons the contemplation of advanced technological solutions. If such crafts were to achieve these speeds in varied environments, it wouldn’t be just about the material but potentially about an entirely new operational paradigm. This leads to the possibility that these vehicles might harness mechanisms to avoid environmental interactions entirely. The concept of interdimensional travel or other exotic mechanisms isn’t just science fiction but could be an intrinsic aspect of their operation, emphasizing a technological prowess far beyond our current comprehension.